|
|
|
NERO Projects H10
Rocket |
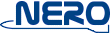 |
The H10 Rocket - The hunt for the European altitude record |
|
|
|
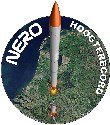 |
NERO has the intention to break the European altitude
record for amateur rockets and bring it to more than 40 kilometres (120 thousand feet). A project team of
ten people is developing and building a two-stage rocket. The goal is to get the English record, which is
set at over ten kilometres, to the Netherlands and to beat it by more than 30 kilometres.
For this purpose, a launch program is set up with three qualification launches before the final attempt.
In order to break this record, NERO is looking for enthusiastic people to strengthen the project team and
for companies, which are willing to support the project with material and otherwise. |
|
|
|
|
1.
|
Sponsors [Top]
[Content] |
|
|
Main-
sponsors |
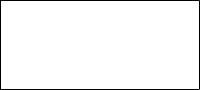
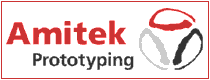 |
|
|
Sponsors |
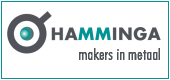
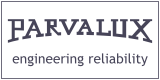 |
|
|
Support-
sponsors |
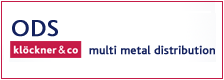 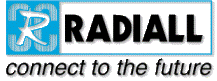
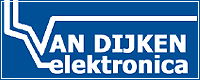 |
|
|
2.
|
Record [Top]
[Content] |
|
|

100KB |
Download the H10 flyer, with a two page description of the project. |
 |
Articles in the Dutch press. |
 |
Pictures of the H10-project. |
 |
The magnificent twelve, the team that makes this dream come true. |
|
|
|
The rocket, called H10, which will be built for the record
attempt, has two motors with a total impulse of over 28,000 Ns. These motors give the rocket an initial acceleration of
23 g and a maximum velocity of Mach 3.
Furthermore, the rocket is subjected to extreme temperatures: aerodynamic heating of the nose cone up to 300 °C,
environment temperatures of –60 °C and air pressure of just 1.6% of the air pressure at sea level. Two parachutes, a
drogue and a main parachute ensure a soft landing. The first stage separation and the deployment of the parachutes is
initiated using pyrotechnic devices. Consider this to be a mechanical part that transfers expanding gasses in motion.
|
|
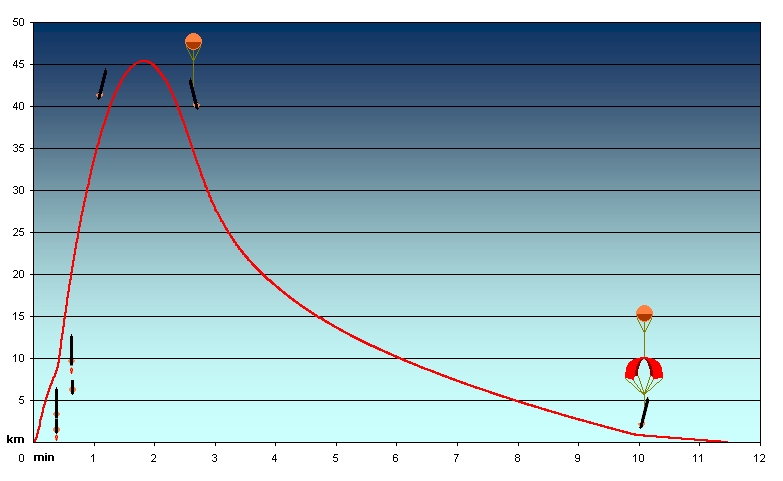 |
|
Remarkable about this record attempt is that the rocket will fly
to this altitude with a full set of instruments. Amongst others a GPS module, a video camera and a transmitter will be
carried on-board. What will make this flight also a very special one is that the H10 rocket will be one of the first
amateur rockets in the world to be equipped with a full-blown situational awareness system. Situational awareness means
that the on-board computer knows the position and the velocity of the rocket in all six degrees of freedom and based on
this, is able to control the flight. In order to realize this, the rocket will have extensive avionics with a large
number of sensors, namely three gyroscopes, a GPS, an accelerometer and a pressure sensor. The used sensors are smart
sensors, which means that the sensor data is being checked and – if necessary – being altered by the accompanying
micro controller. The main flight processor will compare the sensor information of several sensors, in order to
increase reliability. The video images as well as the data are collected by the on-board computers and transmitted to
the ground station using a transmitter.
The ground station receives the video and data signal and splits this up over three screens. On the first screen, a
real-time video image from the rocket will be displayed, on the second screen shows a map of the surrounding area and a
projected position of the rocket and on the third screen vital information about the functioning of the on-board
systems is available and, of course the actual height will be shown! |
|
|
3. |
Design [Top]
[Content] |
|
|
|
 |
|
Nosecone
Calculations have shown that the nosecone will reach temperatures of up to 300° Celsius due to the
aerodynamic friction. Additionally, the nosecone will also have to be permeable to electromagnetic radiation as
the GPS antenna will be located inside the nosecone. To satisfy these not easily reconcilable demands, a new
material will be used for the nosecone called Vubonite. This unique material, developed at the University of
Brussels (Belgium) can be machined like an epoxy yet when dried results in a material with ceramic-like
properties. The nosecone itself has a Von Karman characteristic, as this is the most efficient aerodynamically.
Follow the link and read more about the gyroscopes.
|
|
Electronics module
The advanced electronics module will take up a sizeable amount of the volume of the rocket. Because these
electronics will be exposed to an air pressure of just 0,016 bar, all electronics will have to be tested in a
vacuum chamber. To test the complex electronics a test electronics package will be designed and built with which
a full-system test of an actual flight can be performed. To prevent the powerful RF transmitter causing
interference, the electronics package will be extensively shielded. Follow the link and read more about the H10
avionics.
|
|
Smart sensors, combined with the Main Flight Processor, control four
major events:
1. the separation of the rocket;
2. the ingnition of the second stage;
3. the deployment of the pilot parachute;
4. the deployment of the main parachute.
Follow the link and read more about the flight controller.
|
|
Parachute module
The H10 contains two parachutes: a pilot parachute which stabilizes the rockets as it falls down through the
jet-stream and a main parachute which deploys at 800m (2400 ft) altitude and guides the H10 down to a gentle
touchdown. When the on-board computer fires the pyrotechnical bolt with which the hatch is ejected, the pilot
chute is deployed immediately. Another pyrotechnical device severs a securing line, which allows the pilot chute
to pull out and deploy the main parachute. The upper half of the globe shaped parachute consists of waterproof
parachute fabric, the lower half of gas-permeable gauze. The main advantage of using a ballute is that it cannot
get tangled up since at apogee the air pressure is so low that a normal parachute could get entangled with the
rocket itself! Follow the link and read more about the parachutes.
|
|
Camera module
Contains a small window through which the camera peeks outside at an angle. The camera is positioned in such a
way that the horizon can be clearly seen. Within the team wagers have been struck whether the curving of the
Earth will be visible in the video pictures.
|
|
Transmitter module
The design and development of an antenna, which has a smooth radiating pattern and can be placed inside a rocket
is no small feat. Ultimately, we decided upon a toroidal-type antenna, which is mounted around the fuselage
(circular path antenna). The compartment also contains several lithium-ion cells to fulfill the energy needs of
the rocket. The H10 will be powered by external batteries up until the moment of launch, in order to maximize the
battery capacity during flight. The 10W radio transmitter is the biggest consumer of electrical power in the H10.
The battery pack will be thermally isolated to enable it to withstand the freezing temperatures of -50 to -60 C
(-32 to -50 F) occurring at such high altitudes.
|
|
Rocket motors
The engines are the workhorses of the rocket and are completely designed in-house. Years of development have been
spent on getting them to their current performance level. The engines are even tuned for maximum performance at
the altitude at which they will be operating.
Follow the link and read more about the Penta motors.
|
|
Separation module
The mechanically most complex part on-board the H10 is the separation module, which must eject the first stage.
This part must be strong enough to withstand the high g-forces during launch yet reliable enough to guarantee
successful separation.
Follow the link and read more about rocket separation. |
|
|
|
 |
Launch rail
Launching the rocket in the Netherlands is not an option because of space and safety constraints. We therefore had to
develop a portable, 8 meter (20 ft) long launch tower. The lightweight and modular structure has to be strong enough to
withstand the launch and light enough to be easily transported.
Follow the link and read more about the lightweight NERO launch rail. |
 |
Take a look at the final layout of the more than 10 feet (3.40m) long H10 rocket. |
|
|
4. |
Status [Top]
[Content] |
|
|
|
Several qualification flights will be made in the Netherlands, to
test the developed hard- and software. More than 350 mechanical parts are needed in order to make qualifying and record
flight possible. Especially for the qualifying, a cheap – easy to mount – motor has been developed: the Thrust-18.
When the testing is complete, the high-performance motors will replace both Thrust-motors and the rocket will be ready
to go for the altitude record.
At this moment most of the mechanical parts are ready. Also both
Penta motors are available. Development is focussing on the electronics and the infrastructure (launch rail and
test-bench). Also the ground station needs further development. The motor-problems with the use of the Thrust-18 motor
for the second stage of the H10a will cause a delay from probably one year.
The record attempt will therefore not be earlier than 2007, in a
foreign - to be selected - country. |
|
|
5. |
H10a [Top]
[Content] |
|
|
|
The H10a flight was mend to demonstrate the correct functioning of the mechanics. Due
to high accelerating and deceleration (accelerate after lift-off, decelerate after burn-out and acierate again after
ignition second stage) from the Thrust-18 motor, forces applied to the free standing grain, damaged the grain. As
a result of that the motor produced a thrust vector and the H10a bend sharp to the right. This resulted in a very high
speed at the apogeum, so the parachutes where ripped-off when thrown out. This resulted in a crashed H10a.
New parts for the H10b are being machined at this very time. Also modifications to the
Thrust-18 motor are being defined. These modifications are tested statically and in the next flight of the H11. |
 |
Take a look at the H10a outline. |
 |
Read the flight report of the H10a |
|
|
|
|