|
|
|
NERO Projects H8 Rocket Canards |
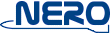 |
The H8 Canards |
|
|
|
The canard control experiment of the H8 consists of a mechanical aspect
(the canard, torque motor and mounting/alignment), an aerodynamics aspect (geometry of the rocket inclusive fins and
canards, calculation of moments and forces), and an electrical aspect (motor controller, safe/arm/inhibit, power
provision). Below, the focus will be on the electrical design aspect of the experiment and the motor selection
criteria. For the pitch axis control two identical canards are mounted at opposite sides of the rocket body. Each
canard is controlled by a dedicated motor. Canard deflections are (for this experiment) programmed to be always in the
same direction. |
|
|
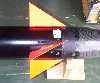
34KB |
Take a look at the canards of the H8. Two of them - positioned in
opposite directions - are controllable, the other two fixed. |
|
|
|
Major design drivers for the canard controller are:
- - Worst case torque to be delivered by the motors, and the duration
of pre lift-off condition.
- - Size, dimension and mass constraints for the motors.
- - Accuracy and speed of the motors.
- - Fail/safe operation.
Typically, for modern fin controller systems, electrical servo
actuators are used. Servo actuators are compact, closed-loop modules comprising an (electrical) motor and associated
gearbox, position/speed sensing device (potmeters/encoders) and an electrical control system that makes the motor drive
meet a given position or speed setpoint. Cheap, compact and lightweight servo actuators are widely used in RC model
cars and aircraft. Unfortunately, a review of the specifications of these servo's points out that they are not
particularly suitable for application as canard controller in the H8. Main objections are:
- they have too large backlash (measured up to 2°) in the gearbox,
- the potentiometers are potentially sensitive to vibration and form
part of the control loop, thereby increasing the risk of noise/spikes,
- the high accuracy devices that are available are too big to fit in
the half diameter of the rocket body.
- they are controlled by analogue pulse with modulation circuits that
are basically inaccurate and sensitive to drift and noise. Professional servo's are very expensive c.q. not
affordable and home-designed servo's require complex mechanical construction.
For the H8 an alternative type of motor has been chosen, namely a step
motor. Each canard is directly mounted on the rotor of a step motor. The step motor is driven by a dedicated step motor
power control circuit. Advantages of the step motor relative to the RC servo's are:
- very accurate positioning and positioning stability (better than
0,1°),
- very fast stepping, typically 1,8 degree in 5 ms,
- simple microprocessor control by providing discrete
clockwise/counter clockwise clock pulses.
The stepmotors also have a number of characteristic disadvantages:
- there is no absolute feedback of angular position so if power is
lost, the absolute position is lost or at least unknown,
- in order to maintain position the coils or 'phases' have to be
powered continuously with requires a high amount of on-board stored electrical energy.
These disadvantages are compensated for by having redundancy in
controller power. |
|
|
|
The figure functional diagram shows the architecture of the step motor
controller.
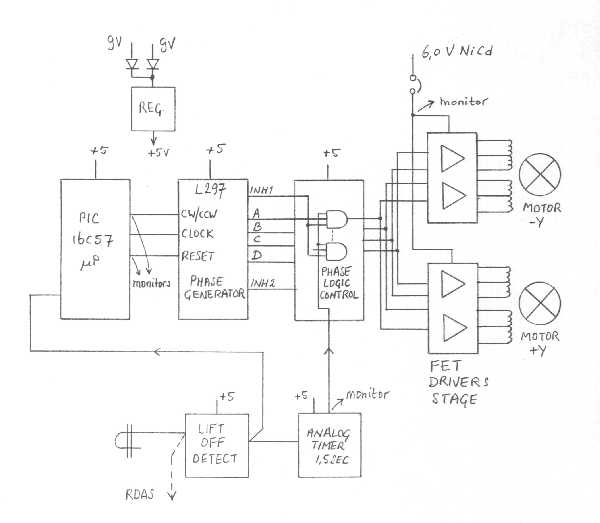
The step motor is from Sany Denki, it is unipolar and delivers a
hold-torque of at least 260 mNs (measured 360 mNs) at a phase current of 1,2 A @ 3,6 V). Each motor has two phases and
there are two motors, so the battery must be capable of providing 4,8 A current. The battery consists of five 1200mAh
high capacity 'penligh-type' NiCad cells. Using very pessimistic assumptions, this battery still provides enough energy
to power the motors for at least 10 minutes.
The driver stage for each motor consists of four power MOSFETS with
low Rds(on). A well-known controller IC type L297 provides the phase switching signals for the MOSFETS. The L297
clock/reset/direction inputs are controlled by a microprocessor PIC16C57 (same type as used in H7 second stage flight
controller). In between the L297 and the gates of the MOSFETS are logic gates that are part of the phase switching
logic and allow overruling the L297 pulses with a canard inhibit or 'holding' signal. This signal is generated by an
autonomous timer circuit that is triggered upon lift-off of the rocket and it forces the step motors to hold their
position during powered flight. At the same time, the microprocessor maintains the hold-state during the rocket motor
burning time. Upon calculated burn-out time, the microprocessor internal timer expires and the canard control
experiment is initiated. |
|
|
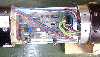
51KB
| A photograph of the experiment controller with the PIC micro controller
in the centre. |
|
|
|
Based on calculations and computer modelling, canard angular
deflections of maximum 10 – 15 degrees (i.e. 5 to 8 steps) in both directions give well measurable and realistic
pitch angle (alpha) variations. The control experiment consists out of 16 sequences of vin movements. For
each sequence is defined:
- number of deflection steps - how many steps of 1.8o
must be made;
- retard time - how many milliseconds between the deflection steps;
- deflection time - how long must the deflection be effective.
The following table shows the used experiment sequence.
# |
Deflection
direction |
Number of
Deflections |
Retard
time [ms] |
Deflection
time [ms] |
1 |
Clockwise |
2 |
10 |
1000 |
2 |
Counterwise |
5 |
10 |
1000 |
3 |
Clockwise |
7 |
10 |
1000 |
4 |
Counterwise |
4 |
10 |
1000 |
5 |
Counterwise |
3 |
10 |
2000 |
6 |
Clockwise |
6 |
10 |
2000 |
7 |
Counterwise |
6 |
10 |
2000 |
8 |
Clockwise |
3 |
10 |
2000 |
|
# |
Deflection
direction |
Number of
Deflections |
Retard
time [ms] |
Deflection
time [ms] |
9 |
- |
- |
- |
- |
10 |
- |
- |
- |
- |
11 |
- |
- |
- |
- |
12 |
- |
- |
- |
- |
13 |
- |
- |
- |
- |
14 |
- |
- |
- |
- |
15 |
- |
- |
- |
- |
16 |
- |
- |
- |
- |
|
Typically, the response of the rocket to deflection steps of various
amplitudes can be measured, at various velocities. After burn-out the velocity of the rocket decreases at a rate of 10
m/s. Therefore the total experiment time is limited tot some 11 to 12 seconds. Upon reaching the apogeum, the
experiment has to be
finished, because parachute ejection is needed for safe recovery. |
|
|

5KB |
Take a look at the H8 Canard Control Software. This software is written in C and
runs on a PIC 16C57 micro controller. |
 |
Link to the Microchip web site, containing more information about the PIC micro
controllers |
|
|
 |
|