|
|
|
NERO Projects H6 rocket H6 Launch procedures |
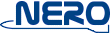 |
The H6c Launch Procedures |
|
|
|
- Assemble Penta-alfa-2 rocket motor completely. Igniter wiring should be
short-circuited.
- Separate motor thrust sensor segment and motor segment from the rest of the rocket.
Disconnect electrical wiring (accelerometer plug and upper coaxial cable). Keep bolts and tooling at hand.
- Mount motor in thrust sensor segment.
- Connect antenna cable to lower coaxial feed through in thrust sensor segment.
- Mount motor plus segment in motor segment using fit-ring at nozzle. Keep motor
compartment vertical while doing this. Igniter wiring should be led through fit-ring.
- Attach the 8 bolts to close motor compartment.
- Apply pre-tension of maximum 100 N to rocket motor using central nut in thrust
sensor segment.
|
|
|
|
H6c installation in launch tower |
|
|
|
- During mounting in the tower the nose tip protection shall remain installed.
- The rocket shall be placed in the tower via the top.
- The rocket shall be oriented in the tower with the hatch pointing downwards (i.e.
azimuth direction of tower), pointing away from personnel performing launch preparations.
- The rocket shall be placed on a wooden block under the fins in order not to damage
the boat tail antenna.
|
|
|
|
H6c arming procedure and final launch
sequence |
|
|
|
Notes:
- before starting this procedure, make sure that all steps which need to be performed
are clear, that necessary systems are operative and that support crew is alert.
- This procedure is to be followed after successfully checking proper timer
functioning using the H6 test box, as part of the rocket final integration activities.
- Start condition: rocket unpowered in launch tower, nose cone removed, SAFE plug
attached, ground segment stand-by, communication link between launch tower and ground segment crew available.
|
|
|
|
1. System powering-up (duration 1 minute)
- Install BAT plug (system powering up) and start manual stopwatch counting at the
same time.
- If a buzzer alarm sounds: remove BAT plug and stop ARM procedure.
2. Checking on-board systems and telemetry test (duration 14 minutes)
- Verify telemetry reception (note: for test purposes this procedure can also be
monitored via the test computer plugged in the EXP connector running the RFA program).
- Verify timer status bits: Count=0 (stop), Lift-off=1 (standby), Safe/arm =0 (safe).
- Optimise telemetry reception in ground segment by adjusting receiver and antenna equipment.
- Inform the crew of other telemetry receivers and allow for optimising equipment
settings.
- Install EXP plug from nose cone.
- Verify analog monitors read-out being compatible with environment (especially nose
tip temperature).
- Verify that stopwatch count is in agreement with telemetry frame. - Verify
controller status is in calibration phase.
- Verify that battery voltage is at least 14 V.
- Verify proper setting of cassette recorder and ground segment computers for
recording data.
3. Arming (duration less than 5 minutes)
- Install ARM plug (a buzzer alarm sounds)
- Verify timer status bits: Count=0 (stop), Lift-off=1 (armed), Safe/arm=1 (armed).
Only the safe/arm bit is allowed to change state from 0 to 1. If this is not the case, stop ARM procedure and leave
rocket.
- Verify igniter status bits (no.1, 2, 3) changing to logic 1.
- Record approximate time of arming.
- Place nose cone and tighten screws.
- Remove nose tip protection.
4. Final countdown and launch sequence (duration less than 10 minutes)
- Return to ground segment.
- Wait for 5 minutes after arming to allow accelerometer internal calibration
(lasting 1 second).
- Verify that controller status enters Pre-lift-off phase 5:02 minutes after arming.
- Inform launch control that synchronisation of launch sequence has to come an end.
- Verify that launch window opens at 6:59 minutes after powering up and start count
down for last 3 minutes exactly 3 seconds later.
- Verify that launch window closes 7:12 minutes after powering up. Note: a launch
window opens every 3 minutes, starting 6:59 after powering up and lasting for 13 seconds.
- At 30 seconds before launch, start recorders.
|
|
|
|
H6c emergency disarming procedure |
|
|
|
This procedure can be followed in all situations where the preparation sequence yields
an unexpected result which might cause a safety risk.
Start condition: any situation with the ARM plug installed.
- Remove the ARM plug, buzzer alarm stops.
- Install the SAFE plug.
- Power down system by removing BAT plug.
If the ARM plug was already removed but the buzzer alarm can still be heard:
- Keep safe distance to rocket (especially hatch).
- Wait for at least 2 minutes before approaching rocket. Stay away from hatch site,
do not move or alter rocket position.
- Open nose cone (if necessary). - Install SAFE plug.
- Power down system by removing BAT plug.
|
|
|
|
H6c disarming and IRM data protection
procedure |
|
|
|
This nominal procedure is to be followed after the flight of the rocket at the landing
site. Start condition: rocket armed, buzzer alarm audible, pyro systems used or apparently failed due to lack of action
during at least 2 minutes.
- Open nose cone by releasing screws. Watch out that the temperature sensor on the
tip is not damaged.
- Remove ARM plug, buzzer alarm should stop.
- Install SAFE plug.
- At this point it is preferable to connect the test computer with the IRMREAD
program to retrieve the IRM data from the rocket. See procedure "IRM readout".
- The rocket may now be powered down by removing the BAT plug.
- Install nose cone and attach sensor protection, or remove nose cone completely by
pulling the EXP plug from its connector.
|
|
|
 |
|